Shuttle Solid Rocket Booster: Key Recovery Facts
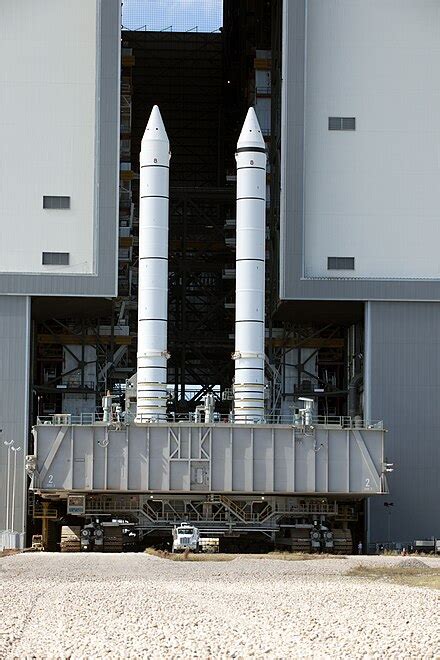
The Space Shuttle Solid Rocket Booster (SRB) recovery process was a crucial aspect of the Space Shuttle program, as it allowed NASA to reuse the SRBs, reducing the cost of access to space. The SRBs, which provided approximately 80% of the thrust required for the Space Shuttle to reach orbit, were designed to be recovered after each mission and refurbished for future use. In this article, we will delve into the key recovery facts of the Shuttle Solid Rocket Booster, highlighting the technical and logistical aspects of this complex process.
Introduction to SRB Recovery
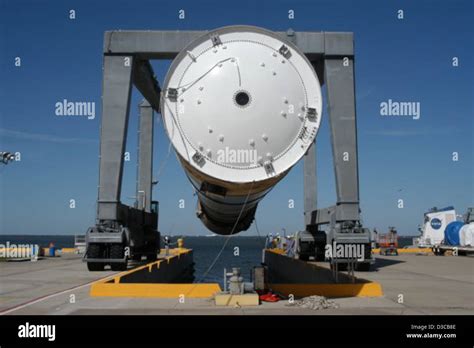
The SRB recovery process began with the separation of the boosters from the Space Shuttle orbiter, which occurred approximately 2 minutes and 12 seconds into the flight, at an altitude of around 150,000 feet. After separation, the SRBs followed a ballistic trajectory, splashing down in the Atlantic Ocean, approximately 140 miles off the coast of Florida. The recovery team, comprising NASA personnel and contractors, would then retrieve the SRBs from the ocean and transport them back to Cape Canaveral for refurbishment and reuse.
SRB Design and Recovery Features
The SRBs were designed with recovery in mind, featuring a number of specialized systems and components. The boosters were equipped with parachutes, which deployed after separation, slowing the descent of the SRBs and stabilizing their attitude. The SRBs also featured a recovery system, which included a drogue parachute and a main parachute, both of which played critical roles in the recovery process. Additionally, the SRBs were designed to be waterproof, with a specialized coating and sealing system to prevent water ingress during the splashdown and recovery phases.
SRB Recovery System Component | Description |
---|---|
Drogue Parachute | Deployed at 15,000 feet, slowing the SRB's descent and stabilizing its attitude |
Main Parachute | Deployed at 5,000 feet, further slowing the SRB's descent and guiding it to the ocean surface |
Recovery Beacon | A radio transmitter that aided in the location and recovery of the SRB |
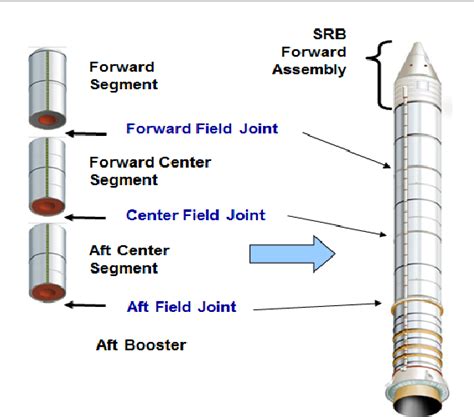
Recovery Operations
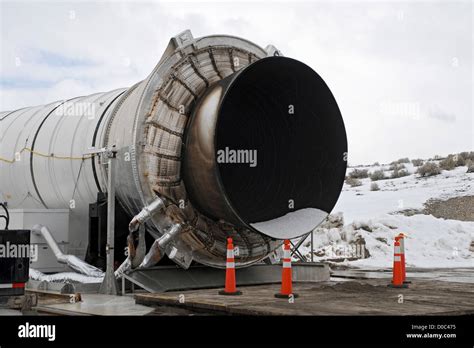
Recovery operations were conducted by a team of NASA personnel and contractors, who used a combination of ships, helicopters, and specialized equipment to retrieve the SRBs from the ocean. The recovery team would typically arrive on the scene within 30 minutes of the SRB’s splashdown, and would then begin the process of securing the booster and preparing it for transport back to Cape Canaveral. The SRBs were transported on a recovery ship, which was equipped with specialized cranes and handling equipment to support the recovery process.
SRB Refurbishment and Reuse
Once the SRBs were returned to Cape Canaveral, they underwent a thorough refurbishment process, which included the replacement of worn or damaged components, as well as the application of a new thermal protection system. The refurbished SRBs were then stored in a horizontal position, awaiting their next flight. The reuse of the SRBs was a critical aspect of the Space Shuttle program, as it allowed NASA to reduce the cost of access to space and increase the efficiency of the program.
The following is a list of key steps involved in the SRB refurbishment process:
- Inspection and cleaning of the SRB
- Replacement of worn or damaged components
- Application of a new thermal protection system
- Reinstallation of the SRB’s recovery system
- Final inspection and testing of the refurbished SRB
What was the primary purpose of the SRB recovery process?
+The primary purpose of the SRB recovery process was to retrieve the Solid Rocket Boosters after each mission, refurbish them, and reuse them for future flights, reducing the cost of access to space and increasing the efficiency of the Space Shuttle program.
How did the SRB recovery system work?
+The SRB recovery system consisted of a drogue parachute, a main parachute, and a recovery beacon. The drogue parachute deployed first, slowing the SRB's descent and stabilizing its attitude. The main parachute then deployed, further slowing the SRB's descent and guiding it to the ocean surface. The recovery beacon aided in the location and recovery of the SRB.
In conclusion, the Shuttle Solid Rocket Booster recovery process was a complex and critical aspect of the Space Shuttle program, requiring precise planning and execution to ensure the safe and efficient recovery of the boosters. The use of specialized recovery systems and components, such as the drogue and main parachutes, was critical to the success of the recovery process. The refurbishment and reuse of the SRBs played a significant role in reducing the cost of access to space and increasing the efficiency of the program.